Saving the USS Texas – the last dreadnought
Battleship USS Texas was decommissioned and commemorated as a museum on April 21st, 1948 – the same day that the Texas Republic won its independence 112 years earlier. The vessel is now drydocked in Gulf Copper & Manufacturing Corporation’s Galveston shipyard undergoing a long overdue overhaul.
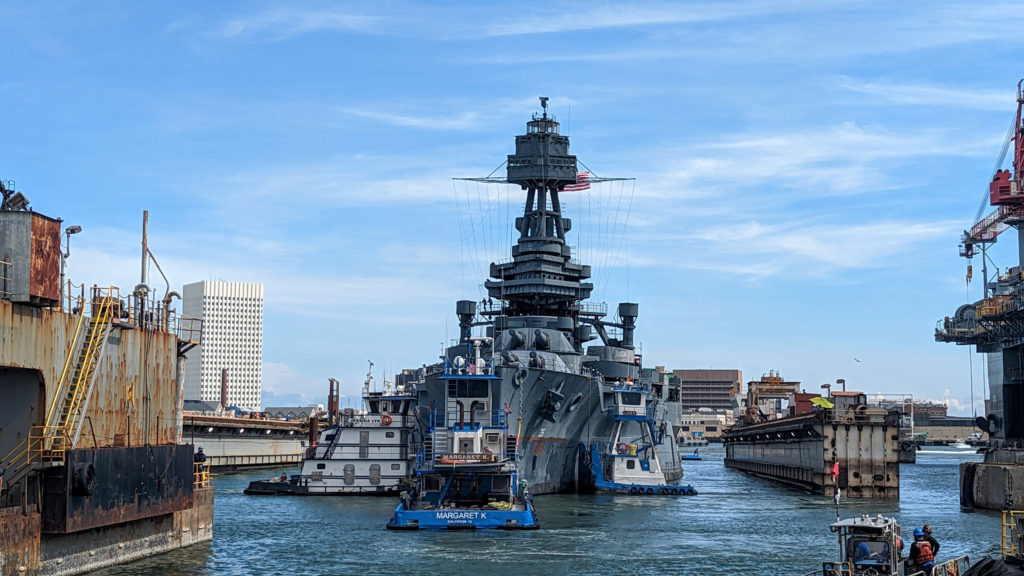
The USS Texas being readied for drydocking
Formed in 1998, the Battleship Texas Foundation (BTF) operates the Battleship Texas under a 99-year memorandum of understanding from the Texas Parks & Wildlife Department (TPWD), which owns the battleship. In 2019, the Texas legislature passed SB1511 directing the TPWD to enter a 99-year lease with a qualified non-profit to operate the ship. In the same session, the legislature appropriated $35 million to fund the hull repair.
As of August 1, 2020, BTF took the lead in the operations of Battleship Texas, with the TPWD retaining an advisory and oversight role.
Preparation for drydocking
The ship closed to the public in August 2019, which was when the BTF, TPWD, and Valkor started work to prepare the ship for drydocking, Valkor Energy Services acting as BTF’s project management and engineering firm.
Resolve Marine Group was contracted in 2020 to prepare the ship for tow to the shipyard. BTF, Resolve, and Valkor worked for six months to drastically reduce the amount of water leaking into the vessel by installing over 750,000 gallons (2,840,000 litres) of expanded foam. The team reduced the leak rate from 2,000 gallons (7,600 litres) per minute to under 20 gallons (76 litres) per minute, making the ship significantly safer to tow.
BTF selected Gulf Copper & Manufacturing Corp’s Galveston shipyard as the repair location. Gulf Copper acquired a floating drydock capable of lifting the battleship out of the water for necessary and extensive hull repairs (see March issue of DryDock p4).
Gulf Copper’s new drydock acquisition was a critical milestone in the Battleship Texas’s $35 million hull repair project as it made the Galveston shipyard viable for the hull repair. In addition, the location of the yard in Galveston significantly reduced the risk of towing the battleship to drydock since the tow was in sheltered waters and the distance was much shorter than other potential options.
Much of the necessary dredging around the battleship was completed by Matthews Brothers Inc in late May. Approximately 23,000 cubic yards of mud (17,585m3) was removed from around the stern of the ship to clear a path for the ship into the Houston Ship Channel.
The Superstructure Rehabilitation Project also began in late May. A $500,000 grant from the Save America’s Treasures grant programme allowed the major backlog of deferred maintenance on the superstructure to be addressed.
The first step was to remove the hazardous materials throughout the foremast, main mast, and aft fire control tower. A&M Environmental and SSCI Environmental were the contractors on this phase of the project to remove lead-based paint and asbestos.
Drydock arrival
June 4 saw Gulf Copper’s newest drydock arrive in Galveston, with its first job the being the repair of USS Texas. The ship was readied for the tow to the shipyard in July. The bulk of the work involved opening and inspecting tanks, taking soundings, carrying out ballast tank integrity checks, and installing temporary lighting to make work safer in areas without functional lighting. It was miserable, tiring, backbreaking work in record-breaking heat and humidity.
At the same time, volunteers helped get spaces clean and organised, moved hoses and opened tank hatches. Resolve delivered pumps, hoses, a portable electrical distribution system (for the pumps) and one of three backup generators for backup power.
Resolve’s pump installation team installed pumps for the tow as leaks could not be avoided. Work done on the ship since 2014 (repairing watertight boundaries and the inner bottom over almost half the ship’s length and foaming the blisters and critical interior tanks) and the final preparation work greatly reduced the overall risk to the ship.
July also saw staff and volunteers fully disassemble, blast/needle gun, repaint and reassemble the first of 10 quad 40mm Bofors anti-aircraft guns. The seals and bearings were replaced, along with a myriad of other odd jobs on the mount.
Ship departure
The USS Texas departed San Jacinto Battleground State Historic Site for repairs on August 31st. The vessel got underway in the early morning and performed far beyond expectations, making it to Gulf Copper Galveston later that afternoon. It was lifted out of the water by the drydock that night, bringing this phase of the project to a close. The battleship was now out of the water for the first time in 32 years, and only the second time since it became a museum in 1948.
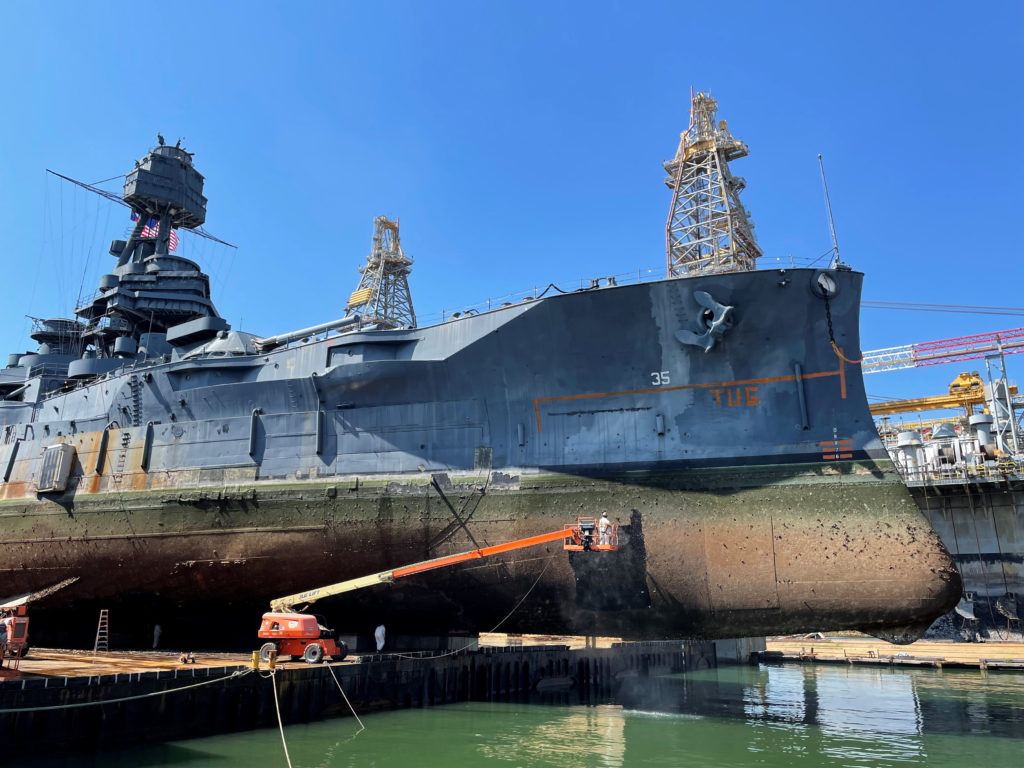
The USS Texas in drydock for the first time in 32 years
Workers soon began cutting sections into the torpedo blisters so that the temporary foam could be removed. This was always part of the plan, and using waterjet cutting, they were able to remove these panels without fire or flame. The marine foam was removed so that hot work such as welding or cutting could begin.
Work began on the forward tanks once they had been cleared, and foam removal in the torpedo blisters continued. The torpedo blisters were removed from a specific point down and were replaced with a slightly modified design, aiming to address some of the issues that had been plaguing them since 1948.
Over the decades, the blisters had largely rusted from the inside out, which could be very clearly seen once cut open. The exterior coating that was applied in 1988-1990 was still intact over most of the ship’s underwater hull, but there was extensive rusting on the interior of the blister tanks.
Removal of the forward section of the torpedo blisters continued during October and thickness gauging and foam removal in the aft section of the ship began.
Workers continued to remove the plates and framing from the starboard side torpedo blisters, and holes in the hull were now visible. The remaining framing was also seriously deteriorated.
Workers gauged the thickness of the hull plating on the aft section of the ship, marking and recording the thickness of each section to assess how best to safely replace or repair these areas.
Foam removal from the starboard side blister tanks reached amidships in mid-October. A rhythm had begun to set in. Foam removal from the internal compartments around the stern was also carried out.
Mid-October saw the first four blister tanks having had their plating removed, with Gulf Copper starting on the fifth. The removal of the blister plating also revealed the section of the hull where the ship’s original torpedo tubes were located. While those tubes had been removed during the 1925-27 refit, there remained the outline of two small squares which were used to seal the hull after their removal.
Work also started to test how easily the 5-inch guns could be removed from the ship. The first step was to see how easily the studs which fix the guns to the main deck could be removed. The nuts which secured them had been removed in anticipation a little while ago, and they were pushed down with relative ease using a porta power hydraulic pump.
The was extensive rust on USS Texas
Port side start
November saw the foam removal reach the end of the starboard blister tanks and the start on the port side blister tanks. The blister tank removal itself went well, and with more of the original hull being exposed, work began on removing sections for replacement.
All the foam in the aft trimming tank was removed and the plating there was removed for replacement as well. A little further aft the plating was found to be in better condition and a doubler plate has been placed on both the port and starboard sides. Work continued on cutting open the hull closer to the pontoon deck to clean out the inner bottom tanks. This opened up the A and B sections of the inner bottom tanks to allow cleaning.
Ship rebuild
The new framing for the torpedo blisters started to go back on in December. The blisters are of a slightly different design, squaring off at the bottom below the waterline.
Work continued moving aft, and any holes in the ship’s original hull (including areas under the blisters) were repaired. New plates were added to thinner areas and smaller pin holes welded up.
More new steel was welded onto the stern of the ship and D12, one of the ship’s more troublesome trim tanks, received much-needed new steel. The structural repairs carried out in the 2010s were now finished as the frames were now welded to the new skin.
January saw the addition of new framing for the torpedo blisters being stopped on the starboard side. Any new frames are now in modular form, consisting of about nine frames each, produced away from the dock in the shipyard’s fabrication shop.
Staff and volunteers work on both the 5-inch and 3-inch guns in the warehouse, with new primer going on the first 5-inch/51 gun.
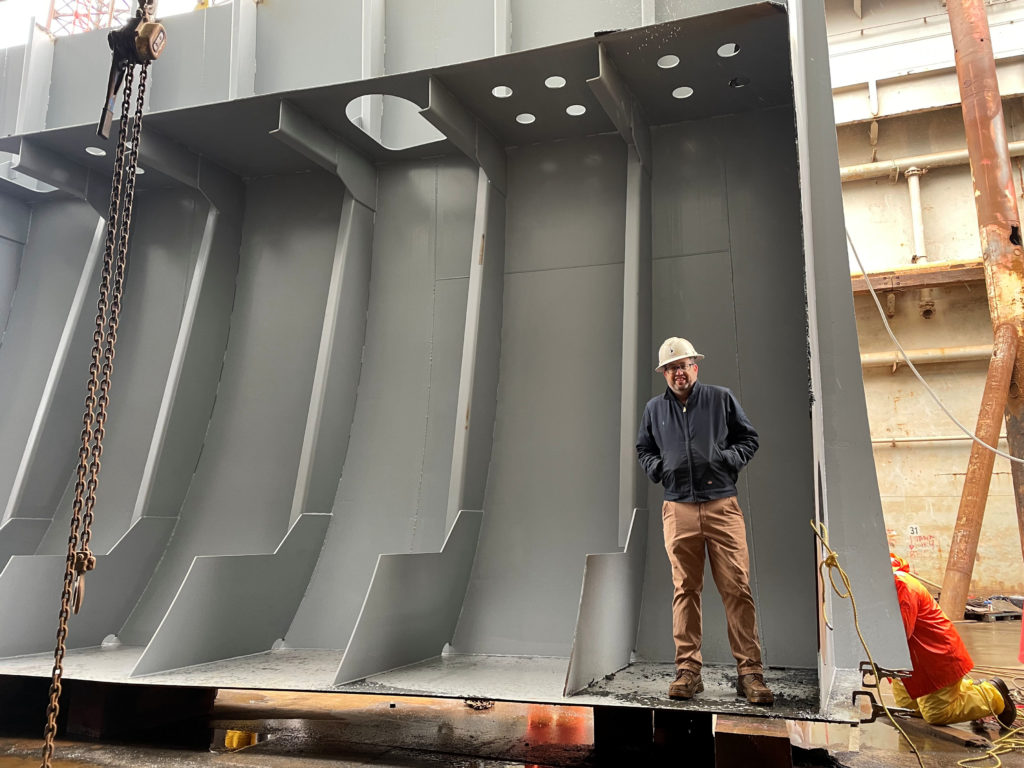
The new frames in modular form
First module
The first torpedo module arrived on the dock floor ready for installation at the end of January.
The middle of February saw the starboard side ship’s hull being temporarily primed.
Mid-March saw three torpedo blister modules installed on the starboard side, with the forward sections now almost entirely plated up. The inside of the blisters and the ship’s hull were coated to increase longevity.
Foam removal from the port side blisters was now also complete.
In April, the first frames of the port side blister were installed. Just like the starboard side, the forward most section was built frame by frame, with the bulk of the blister being built using the module approach. The last three 5-inch guns were removed from the ship and transferred to the warehouse for restoration.
New plating is continuing at a pace on the ship’s stern. Any steel that comes off the ship and is deemed worthy will be used in future fundraising. Battleship Texas Foundation has already started making prototypes of the new products it will be offering in its store.
If you want to know more about the rescue of the drydock, you can find it here
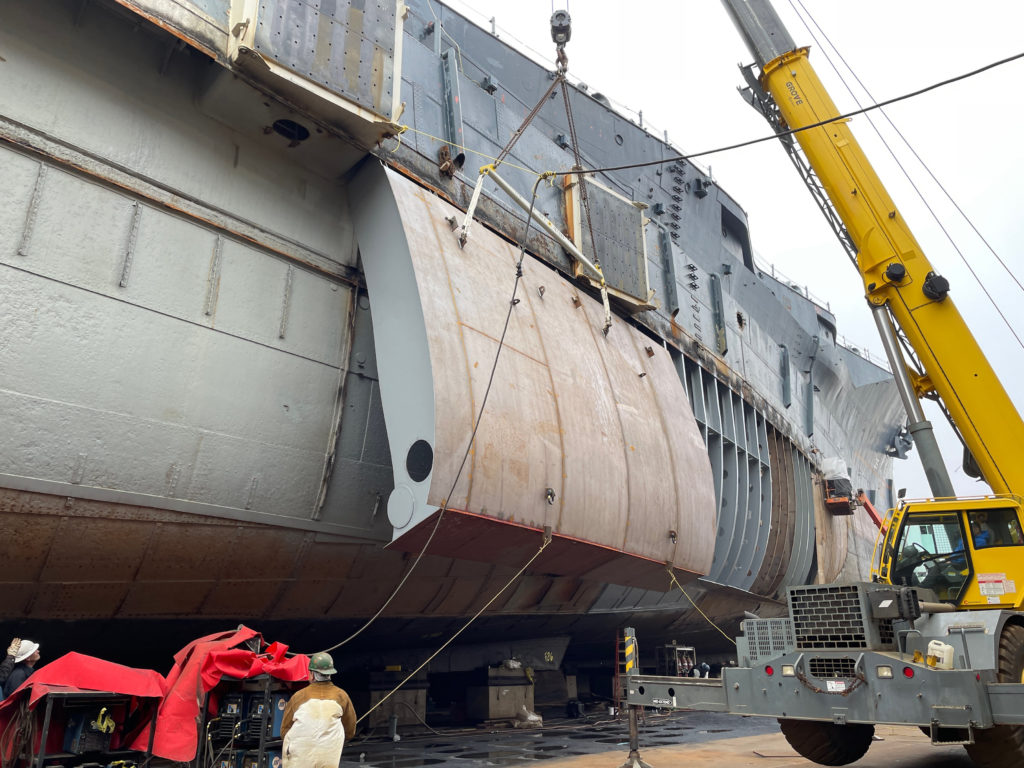
Replacement of the hull plating underway on USS Texas