Spotlight on Cruise & Ferry ship repairs
Busy starts to the year at Remontowa, Fincantieri and SMS, A&P Falmouth sees the largest passenger ship visit for 6o years, Survitec secures an order for nitrogen system installations on an LNG-powered cruiseship and Trimline upgrades the Oasis class ships.
A busy start to the year with ferry repairs at Remontowa
Hurtigruten Group entrusted Remontowa Shiprepair Yard with upgrading three of its Norwegian Coastal Express ferries: the Nordnorge, Nordkapp and Polarlys. After conversion the first vessel left the shipyard in May 2022, the second in November 2022, and the final one in March 2023.
A key challenge was to complete the entire project on time, as the converted ships had to return to their routes on scheduled dates. This required the shipyard to organise the production and logistics process efficiently. Remontowa had already met this condition when converting the first ship, MS Nordnorge, which the shipowner appreciated. In addition, a large scope of the ferry’s class renewal work was carried out during the conversion project.
All the vessels have undergone a similar scope of upgrades. They have been retrofitted with a Selective Catalytic Reduction (SCR) system to reduce the nitrogen oxides in the exhaust gases. As a result, CO2 emissions have been reduced by 25% and NOx by 80%. New exhaust gas boilers were installed to utilise exhaust gases more efficiently. In addition, each vessel has been fitted with a new waste treatment plant with collecting/holding tanks. A new bulbous bow section has also been fitted to the hulls to reduce fuel consumption.
Remontowa has also upgraded and refreshed the passenger spaces. After the conversion, the comfort and functionality of nearly 100 cabins on three decks of each ship have been enhanced, with furniture, wallpaper, lighting, flooring and carpeting replaced.
Repairs/retrofits
In December 2022, the Mont St Michel, operated by Brittany Ferries, entered Remontowa. The vessel underwent a comprehensive drydocking, one of the largest in the last 20 years.
The main and auxiliary engines were almost completely dismantled and after a thorough overhaul in the shipyard workshop, including mechanical treatment of all engine blocks, regained full power and efficiency. All equipment in the engine room, including pumps, compressors and coolers, were also overhauled. Much work was focused on electrical systems, including motors and fans. Pipelines were comprehensively inspected, with some sections replaced. Propulsion system components were overhauled, including shaft lines, rudder gears, propellers and bow thrusters. The machining of the dismantled stabilisers as part of their reconditioning greatly enhanced their operation. Steel in the tanks was also replaced and the hull, car decks and ramps underwent maintenance.
Pont Aven was the next French ferry to call at Remontowa in Q1 2023. One of the priority tasks was retrofitting it with a BWT system. The ferry has also been fitted with new telecommunication systems, including laying fibre-optic cables and modifying IT equipment. Pont Aven has also undergone an overhaul of the main engines and auxiliary gensets.
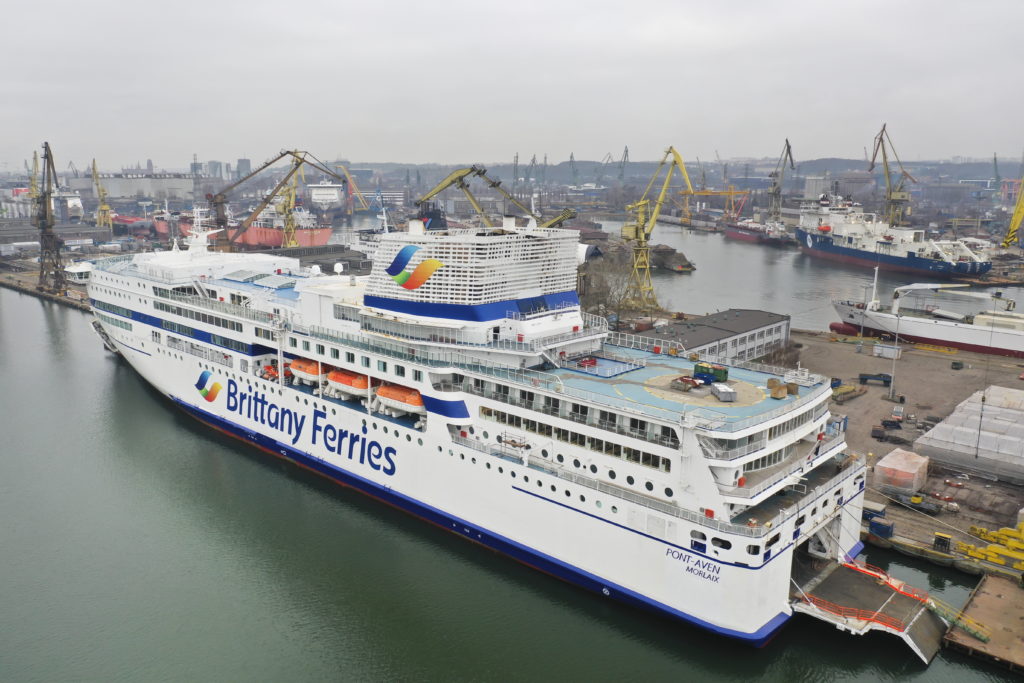
Pont Aven called at Remontowa in Q1 2023
TT-Line repair
The Marco Polo ferry, converted in Remontowa a few years ago, has recently returned for drydocking. The yard revitalised the entire steering system. The components underwent comprehensive mechanical treatment after being dismantled and transported to the workshop. That included the rudder gear, the rudder stock and two rudder blades, as well as the starboard shaft, the propeller hub and blades and the stabilisers on the port and starboard sides. The main engine and one of the auxiliary ones were also overhauled. The engine room wasn’t ignored, and equipment such as shaft generators, electric fan motors and pumps (scrubber and ballast) were repaired.
Intensive maintenance was done on the three car decks, where around 110 tonnes of steel were replaced. The ‘tween deck and stern ramps also underwent maintenance, with a standard overhaul of the trays.
The repairs, combined with a steel replacement, also included the ferry’s bulbous bow, the void spaces on the port side, and the plating in the freshwater tank area, which received steel inserts. The bilge, seawater, cooling, fire and sprinkler systems have been comprehensively overhauled, including partially replacing the relevant piping in the engine room.
Stena Line overhauls
In December 2022, Stena Livia came to Remontowa. Along with a major scope of repairs, the main work was maintenance and painting the ferry with a silicone coating.
In the first days of February 2023, the Stena Flavia arrived and moored opposite another Swedish ferry, Stena Nordica, whose conversion was then underway.
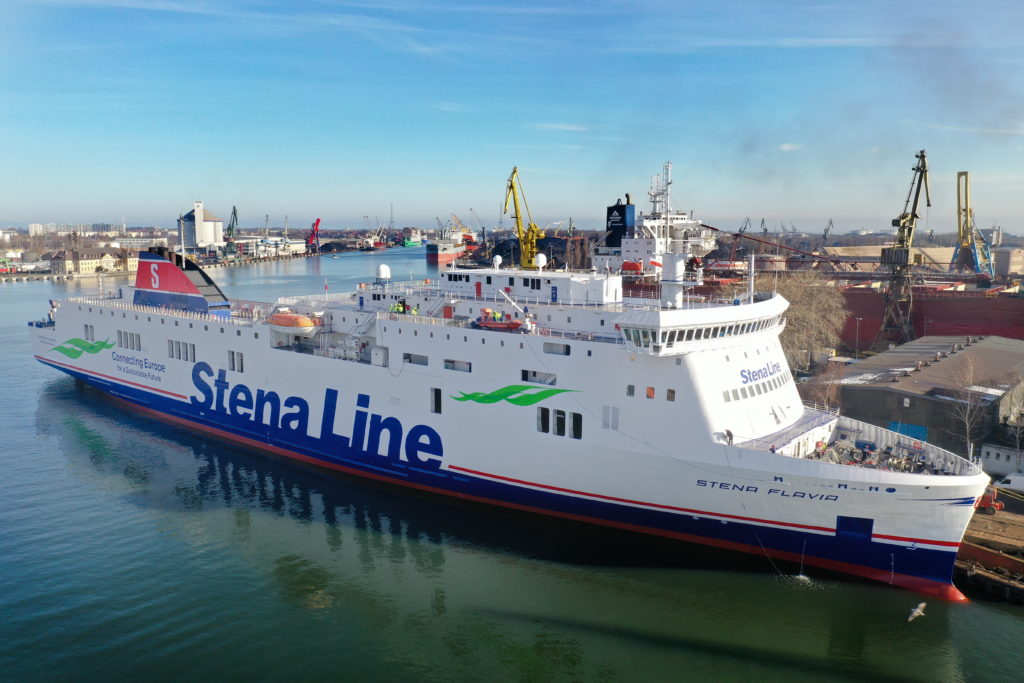
The Stena Flavia arrived at Remontowa at the beginning of February
On the drydocked ferry, Remontowa replaced the seals after pulling out the two shaft lines and taking measurements. The rest of the propulsion components, such as stabilisers, bow thruster and propeller blades, once dismantled, were transported to the shipyard workshop, where comprehensive overhauls were carried out.
The yard also overhauled the overboard valves and replaced the outlets. Much steelwork was done in the funnel area, where the supports and fixing points were replaced.
Another major job was replacing the coating on the underwater section of the hull. The existing coating system was removed using UHP (ultra-high-pressure water blasting). Then several layers of a new silicone paint were applied. In addition to the job mentioned above, Remontowa performed mechanical works and pipeline modifications on the Stena Flavia.
DFDS modernisations
In Q1 2023, Remontowa carried out modernisation projects on Regina Seaways, Princess Seaways and Sirena Seaways. The first vessel was retrofitted with a BWT system. The steering components were also overhauled. The work included shaft lines, rudders, rudder stocks, propellers, hubs and a bow thruster, which underwent mechanical treatment in the workshop.
On the internal ramp connecting the two car decks, the yard mounted a new steel element supplied by the shipowner after cutting out a previous one. One of the ferry’s decks underwent maintenance in the covered and open areas. In addition, steel in several places was replaced and a standard valve overhauled. The underwater part of the hull was coated with silicone.
The RoPax Princess Seaways underwent an intermediate survey at Remontowa. Maintenance and inspection were carried out on many items of equipment. Steel was replaced in the bow area, on the stern ramp flap and in the exhaust system. The yard also applied silicone paint to the underwater part of the hull.
Another DFDS RoPax vessel, Sirena Seaways, had Remontowa retrofit a BWT system. Most of the important equipment was installed in the forward part of the ferry in a special compartment, the scrubber room. The site is significantly remote from the engine room, so connecting them by pipeline was a challenge.
Busy start to 2023 for Fincantieri
2023 has seen a busy start for Fincantieri’s repair and conversion shipyards, with some projects continuing from last year and additional works entering its facilities at Palermo and Trieste, signalling a positive trend for the ship repair and conversion sector in the Mediterranean.
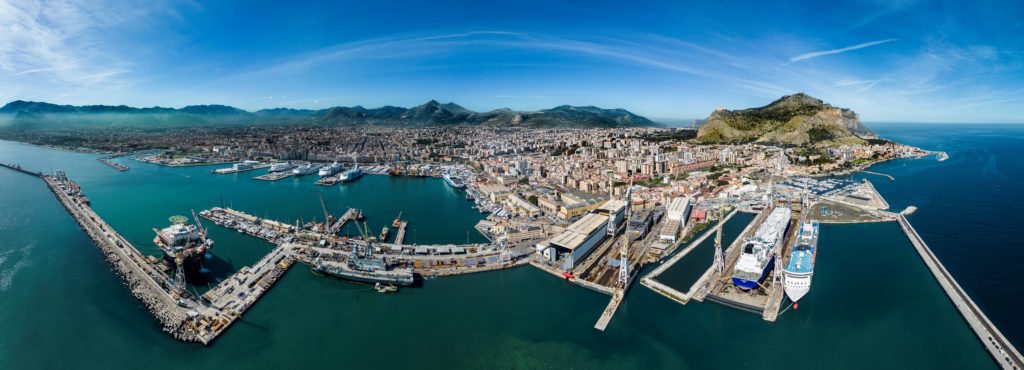
Fincantieri’s Palermo yard has also had its fair share of varied and interesting projects this year
The Fincantieri Trieste facility has an excellent record of accomplishing cruiseship upgrades, with several complex projects completed over the last few years. Major works are now underway on the 250m Crystal Serenity and 238m Crystal Symphony. These two cruiseships, under the ownership of A&K Travel Group, which acquired the ships and brand in 2022, are currently undergoing an extensive interiors modernisation programme.
During November 2022, German cruise line Aida Cruises’ AIDAblu was at the Trieste shipyard for a two-week drydocking, during which hull treatment, steel and engineering works were completed. The RoPax A Galeotta, built at Cantiere Navale Visentini Italy and operated by Corsica Linea, left the yard in mid-November after several weeks stay for drydocking, hull coating and engineering maintenance. This vessel is powered by liquefied natural gas and was bunkered with LNG prior to leaving the Trieste facility for service between Marseille and Corsica.
Superyachts coming to the fore
Along with cruiseship and commercial works, superyacht repairs and upgrades remain a key target market for Fincantieri, especially at the Trieste yard which is increasingly coming to the fore in this sector. The facility has enough capacity to handle larger superyachts and draws on an established network of specialist contractors and suppliers that can be quickly mobilised for works on superyacht projects. Over the last months three superyachts, the Alaiya (111m), Brother Brancusi (66.8m) and Quattroelle (86.11m) have all undergone repair and upgrade work at Trieste, with both Alaiya and Quattroelle requiring a period in drydock, while the work on Brother Brancusi was completed afloat.
The shipyard in Palermo has also had its fair share of varied and interesting projects this year. The Princess Cruises vessel Enchanted Princess arrived at the yard in the last week of March for various works, including drydocking in the large 400,000dwt graving dock and scheduled for a mid-April departure. During this period, an Air Lubrication System (ALS) is being installed which is expected to generate significant savings in fuel consumption and carbon emissions by reducing hull drag.
From the offshore sector, the cable-laying vessel Living Stone left Palermo after drydocking and hull treatment work late in 2022, while the Arendal Spirit arrived at the yard in December 2022 for afloat repairs. Work on this vessel includes complex thruster repair and maintenance procedures. The Palermo shipyard has very deep drafts down to 25m, which makes it well suited for offshore unit projects, such as working on azimuthing thrusters.
Palermo shipyard drydock accommodated its first LNG tanker of 2023 during March. The Grace Emilia was repaired and left the yard at the end of the month.
SMS scores an early hat trick
The SMS Group, based within the ABP Southampton footprint in the port of Southampton, has won three major fast-ferry refits in the first few months of 2023. The business continues to support the internationally-based fleet of high-speed craft.
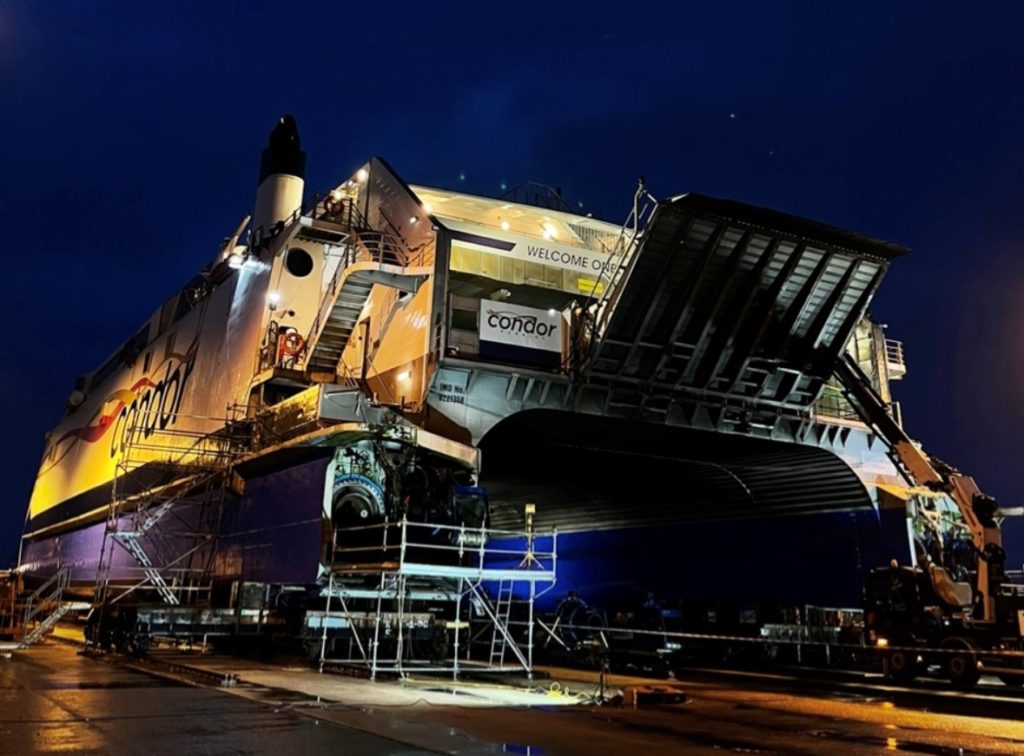
The SMS Group has won three major fast-ferry refits in the first few months of 2023.
The SMS Group has a fantastic pedigree in the repair and maintenance of fast ferries and high-speed craft. The team in Southampton has recently undertaken work in Denmark, France and Belfast across three very different projects.
In Denmark, the company has supported the technical management of a major fast-ferry refit on behalf of the ship’s builder. In France, on behalf of Condor Ferries, the operator, it has undertaken a major package of mechanical works on the shiplift in Cherbourg. SMS is also working at Harland & Wolff, in Belfast, supporting the overhaul of the stern gear on a 102m vessel for Irish Ferries.
“Our knowledge and experience in the repair, maintenance and overhaul of jets, shaft lines, ride control units and high-speed diesels speaks for itself; and now we’ve expanded the team in Southampton we’ve the bandwidth to undertake projects simultaneously – both here in the UK and overseas,” says Nicholas Warren, Commercial Director.
The SMS Group’s expertise includes mechanical and structural repairs, and also interior refurbishment.
“In a separate project, we’re currently undertaking works in Liverpool for the Isle of Man Steam Packet Co – a major package of interior refurbishment and upgrades onboard a 98m fast ferry,” explains Warren. “The work includes an interior upgrade, enhanced galley and servery, and an upgraded first-class lounge”.
The SMS Group trades from eight locations in the UK offering marine engineering and interior outfit solutions both nationally and internationally.
Bolette at A&P Falmouth
A&P Falmouth has completed a multi-million-pound programme of work on the largest passenger ship to visit the facility in over 60 years. The Bolette is Fred Olsen Cruise Lines’ flagship vessel and carries up to 1,338 passengers and 645 crew.
The Bolette entered drydock for a 13-day refurbishment, including maintenance to the ship’s Azipods and bow thrusters as well a new application of underwater paint.
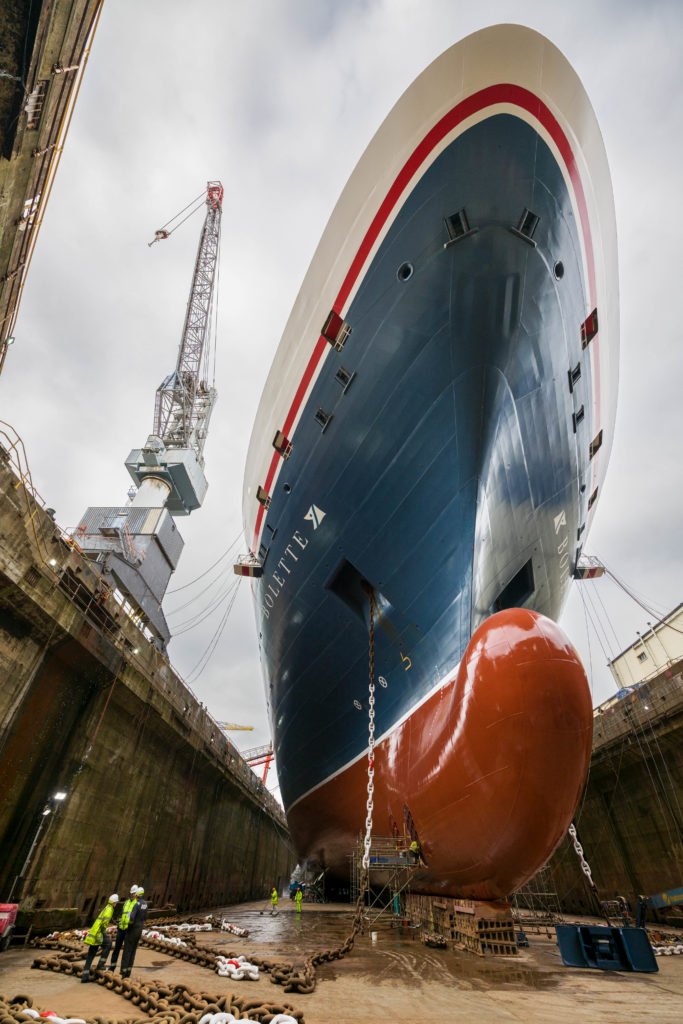
The Bolette is the largest passenger ship to visit A&P Falmouth in over 60 years
Over 500 members of the A&P workforce and supply chain worked around the clock to support this contract. Additionally, 32 apprentices had the experience of working on the Bolette.
It is the second time in 12 months that Fred Olsen has chosen to dock at A&P Falmouth, with fellow ship Balmoral completing a programme of work in May last year, which included steel inserts, ship side valves, tunnel thruster overhaul and underwater paint.
“A&P was delighted to welcome Bolette to the facility – and facilitate a visit from Peter Deer, Managing Director of Fred Olsen,” says Mike Spicer, Managing Director of A&P Falmouth. “The visit provided a fantastic opportunity to showcase our capabilities – A&P’s location in the southwest makes it an ideal facility for cruise ships operating in this area.”
He went on to say: “Contracts such as these make a significant economic contribution to the prosperity of the southwest and helps to support our workforce and apprenticeship programme. We look forward to continuing our partnership with Fred Olsen Cruise Lines over the months and years to come.”
David McGinley, CEO said: “It is fantastic to welcome Fred Olsen’s Bolette into A&P Falmouth.
“Projects such as these help us to sustain our workforce, apprenticeship programme and supply chain which drives prosperity and adds real social value to the southwest of England.”
Alternative fuels transition
Maritime Protection, a brand of global survival technology solutions provider Survitec, has secured an order for a set of nitrogen systems for installation on an LNG-powered cruiseship.
The company, which has hailed the contract as significant, has welcomed the opportunity to support the cruise industry with its transition to alternative fuels. In particular, to offer expertise on the implementation of IG (inert gas) systems as an important safety measure.
“This order signals Survitec as a trusted partner to the cruise industry,” explains Mark Clegg, Managing Director, Fire Systems, Survitec. “While our Inert Gas (IG) systems have already gained widespread use in other ship types, the passenger ship sector has only recently begun to explore the technology. From our standpoint, a cruise ship is no different from any other vessel. Nevertheless, this latest contract win allows us to expand our market, and we anticipate more orders as more passenger vessels shift towards cleaner fuels.”
The scope of supply is for two nitrogen generators, feed-air compressors, valves, and control cabinets. Scheduled for delivery in 2025, the 51,950gt newbuild is the first cruiseship for this Japanese owner to be built in Europe. There is an option for a second vessel.
About 10 LNG-fuelled cruiseships are currently in operation, with a further 25 set to join the global fleet over the next five years. Engines operating on LNG, ammonia and methanol in particular, require an N2 system for safety reasons. “Nitrogen is used to purge the fuel gas system before and after engine start-up or when any maintenance work is carried out. It creates a safer, more stable environment,” explains Rune Moseidjord, Sales Manager, Maritime Protection. “It is crucial for any passenger ship going down the alternative fuel route to have a low maintenance, reliable, affordable N2 system. The benefit of our IG systems is that each one is engineered to order, designed to meet the requirements of each individual ship.”
Maritime Protection’s nitrogen systems are easy to install and fully automatic with PLC control. Furthermore, the system can be supported by the brand’s remote assistance offer, which enables support services, such as technical support and troubleshooting, to be delivered remotely.
“We’re seeing an increase in passenger ship operators specifying vessels with engines capable of running on LNG,” says David Welch, Shipyard Sales Manager (Global Cruise), Survitec, commenting on the cruise sector’s wide acceptance of LNG bunkering. “The sector is really pushing the green agenda as some destinations are now limiting the size and number of ships burning heavy fuel oil, but shipowners must consider the fire risk. The consequence of a fire from these alternative fuels can be substantial. This requires a higher focus on fire prevention through the use of inert gas systems and very early detection through the monitoring of gas pressures and temperatures.”
He continues: “Our Head Start initiative was designed with this in mind; we support ship owners and work with them from first designs to scope their requirements and design a total fire protection and safety management package. We can help them to set up their vessel for a lifetime of safety at sea.”
Survitec also supplies nitrogen IG systems to cruise and RoPax ferries running on LNG as a marine fuel, having recently secured orders from shipyards in Poland and Turkey.
Trimline upgrades Oasis class
Ride-on squads from marine outfitters Trimline are currently carrying out works onboard three Royal Caribbean Oasis Class ships, converting current jazz venues into a smoke-free casino space.
The clubs were identified as an ideal space for a transition into smokeless casinos, offering guests an alternative smoke-free option while on board.
The work is being carried out while the ships are in service, which has involved meticulous pre-planning and attention to detail to ensure there is minimal disruption to crew and guests.
The teams onboard each ship comprise demolition and removal, joiners, electricians, decorators and labourers who are working alongside data, IT and casino-commissioning experts.
The works on each ship were due to take two weeks to complete, with the final ship scheduled to be completed on 15 April.