Preventing drydock accidents: A three-pronged approach
In the past four years, at least four vessels have capsized during drydocking operations. These include the mega yacht Nero; a United States Navy research vessel, Petrel; a Dutch tall ship, Europa, and a motor ship, Kind, explains Robert Taylor, Principal Engineer – Shipyard Solutions, Bardex Corporation.
Robert Taylor is an expert in global engineering and maritime applications with more than 30 years of experience on multi-million-dollar projects. He specialises in the design and fabrication of heavy steel structures, steel erection, heavy lift applications and large multi-discipline project management. He holds a Bachelor of Science in Civil Engineering from Virginia Tech and is a Registered Professional Engineer: State of California.
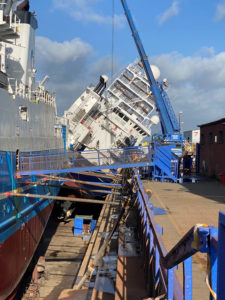
The US Navy research vessel Petrel capsized in drydock in Leith, Scotland
In all the above cases, there were initial cursory reports by local media of serious injuries and damage to the ships. Because there are no regulatory requirements for investigating and reporting such incidents, little else is widely known about the frequency of such occurrences, the full extent of losses, or the causes and contributing factors.
Nevertheless, accidents like these indicate problems with long-standing blocking practices, such as using timber blocks. Shipyards can improve upon these practices by adopting modern alternatives in design tools and engineered materials.
Q. Why are timber blocks used?
A. Timber blocks do two things well: They avoid scratching a ship’s paint and causing dents, the way other common materials, such as steel, would. Another desirable quality is their ability to conform to the hull; however, they do not do this uniformly, reliably or predictably.
Timber blocks do not compress at a quantifiable, consistent rate, and once compressed, they do not rebound, or adjust, in response to load changes. So, when loading conditions change, some blocks might not actually be bearing any load. Obviously, this compromises the stability of the ship.
Q. What are elastomeric pads and what are the advantages of using them?
A. Elastomeric pads are commonly found in buildings located in earthquake-prone areas, acting as dampers or shock absorbers. They translate to the shipyard exceedingly well.
Elastomeric pads compress and rebound at a reliably predictable rate during all phases of vessel docking and transfer and can be used with any type of vessel support system. Furthermore, they are impervious to seawater, so they require no maintenance and pose no risk of pollution.
Q. What other alternatives are there?
A. Another alternative to blocks is hydraulic fluid beds. However, compared with elastomeric pads, these are far more complex to implement and maintain, less reliable, and, because the hydraulic components must be submerged with the platform, there is the risk of fluid leaks and fluid contamination.
Q. What are the problems with blocking plans?
A. Blocking plans often contain fundamental errors in loading and support assumptions. Some methodologies do not adequately account for two key factors: the structure that supports the blocks and external forces, each of which affects the centre of gravity of a load.
Supporting structure
Blocking load distribution differs depending on whether a vessel is on a shiplift platform, floating drydock or a graving dock. Structural engineers refer to this type of situation as a rigid beam on an elastic foundation. Simply put, when something very stiff is supported by something less stiff, it becomes difficult to understand the load path. As the blocks apply pressure to the supporting structure, some compress more than others, altering the centre of gravity of the load. If the centre of gravity changes enough, a ship can become unstable and overturn.
External forces
The conditions that exist when a blocking plan is put in place often change while a ship is drydocked for refit. In addition to dynamic weather conditions, people, parts and equipment move within and around the ship, all changing the centre of gravity. When the cumulative effect of these changes is great enough, the ship will overturn.
Without a doubt, these are complex problems, and solving them requires modern computational and predictive tools that are largely absent in the shipyard industry.
Q. What is the alternative to the long-standing blocking plan?
A. Finite element analysis (FEA) is a computerised method for predicting how a complex object or system will behave under real-world conditions. It is used widely in the aerospace, automotive and building industries, among others, to find and correct system weaknesses, determine safety margins, and identify optimal designs.
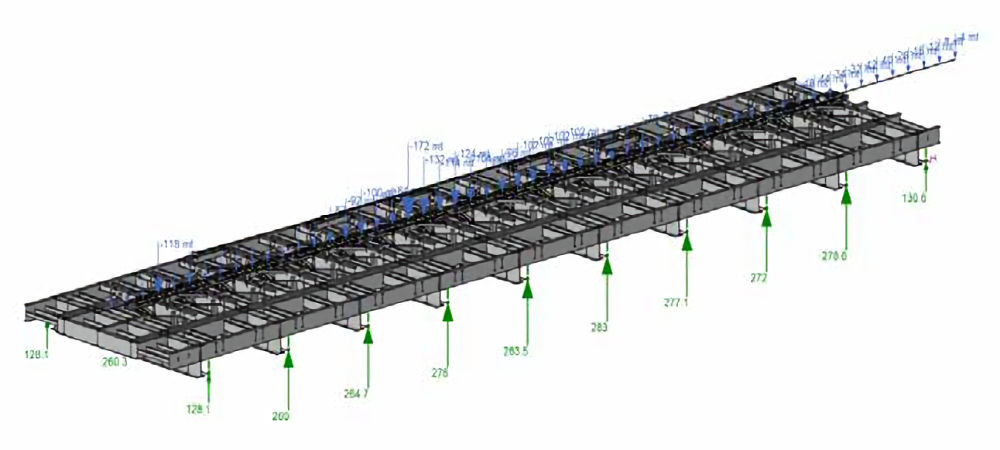
Platform and cradle docking FEA simulation: Keel Lad and reactions, Stern in docking FEA simulation
In the context of a shipyard, FEA addresses the risks and uncertainty inherent in current blocking practices. FEA requires specialised knowledge and a detailed understanding of the structural system supporting the vessel. We recommend that our clients perform this more detailed analysis when one or more of the following conditions is present:
1) A facility is docking a particular vessel for the first time. The owner may have excellent information from prior dockings at similar facilities, but often this is not the case due to changes that occur over time and other external factors that impede reducing the weight and improving the trim of the vessel prior to docking.
2) The vessel approaches or exceeds the system’s Nominal Lift Capacity in total weight or maximum linear density.
3) The vessel has unique features that complicate the docking plan and cause load concentrations. Examples include sonar domes, moonpools or large overhangs at the bow or stern.
4) Modifications are planned that may change the centre of gravity or weight distribution of the vessel.
5) The shipyard is in an area that experiences high seismic activity or extreme weather events like tornadoes, hurricanes, and tropical storms.
6) The docked vessel will be transferred across different civil or structural support systems.
Q. How do you think things can be improved?
A. When a bridge or building collapses, a forensic investigation is performed to determine what happened, and the findings are then published for engineers to review. Depending on the factors that contributed to the failure, changes can be made to codes, structural designs, processes, materials, training, and so on. In other words, the engineering community has access to the information it needs to analyse the problem and look for solutions for avoiding similar incidents in the future.
This is not what unfolds after a shipyard accident. Although there may be an investigation, its focus is on insurance and legal matters, not on problem-solving. This is a missed opportunity to improve safety and reduce the risk of losses for shipyards and shipowners alike.
Together with more widespread use of modern alternatives in design tools and materials, implementation of regulatory standards for investigating and reporting the causes of drydock accidents can go a long way in preventing ships from reaching their tipping points.