Waterjet cutting allows for environmentally friendly ship recycling and green steel production
In Germany, two pilot projects are under way for the dismantling of obsolete ships with the environmentally friendly waterjet abrasive suspension system. ANT AG’s high-performance, energy-efficient technology achieves remarkable results in compliance with all international requirements for sustainable ship recycling. In addition, it facilitates the recovery of valuable raw materials, which can be used for the production of climate-neutral steel.
In the light of the ongoing shift to emission-free shipping and a growing world merchant fleet, a significant increase in scrapping activities is expected within the next 10 years. The number of vessels to be recycled is projected to grow from 7,780 ships in the last decade up to 15,000 ships with a transport capacity of 600 million tons (last decade: 285 mio tons). Furthermore, new regulations stipulate clean and safe ship recycling. At the same time, the steel industry, one of the world’s main emitters of CO2, faces the challenge of reducing emissions by about 30 per cent by 2030 in accordance with the Paris Climate Agreement of 2015. Around 85 per cent of CO2 emissions in steel production occur in the blast furnace. Scrap steel from ship dismantling provides a notably sustainable option, as it can be fully recycled without any loss of quality. Around 1.6 tons of CO2 per ton of recycled steel can be avoided.
Suspension jet cuts solid steel
In June 2022, a pilot project for the virtually emission-free dismantling of ships has started in Kiel, using ANT AG’s globally patented waterjet technology. A similar pilot project is planned in Bremen. The waterjet abrasive suspension system can produce a high-pressure jet that cuts steel plates of up to one meter thickness at 2500 bar. 10-millimeter-thick ship steel can be cut at a speed of about 2 meters per minute. The extendable cutting system is remotely controlled and positioned close to the steel to be cut. The cutting jet consists of a suspension of water and added abrasive. Even multi-layered materials and structures with cavities such as fixtures, insulation and cladding can easily be cut.
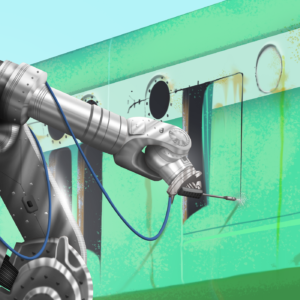
The high-pressure abrasive waterjet works from the outside to the inside and cuts steel plates of up to one metre thickness into pieces of any size.
Environmentally friendly, safe and flexible to use
Waterjet cutting produces neither any CO2 nor any fumes or slag. In addition, the suspension water jet does not create any sparks, which reduces the risk of fires and explosions. The contactless cutting process does not generate any heat nor material deformation. In contrast to conventional methods, the water jet can also work from the outside to the inside, so that no slag or paint chips can contaminate the surroundings and challenging materials remain safely inside the ship from where they can be collected and disposed of. Even gas tanks made of invar, a high-value iron-nickel alloy that features a high length stability during temperature changes, can be cut into any size. The waterjet abrasive suspension system is flexible and can be remotely operated from a distance of up to 500 meters.
International requirements for sustainable ship recycling
Every year hundreds of ships around the world are decommissioned and scrapped. The steel recovered from these ships is a valuable resource. Therefore, global regulations such as the Hong Kong International Convention for the Safe and Environmentally Sound Recycling of Ships, which will enter into force on June 26, 2025, and the EU Ship Recycling Regulation (EU SSR) advocate environmentally friendly ship recycling and safe working conditions.
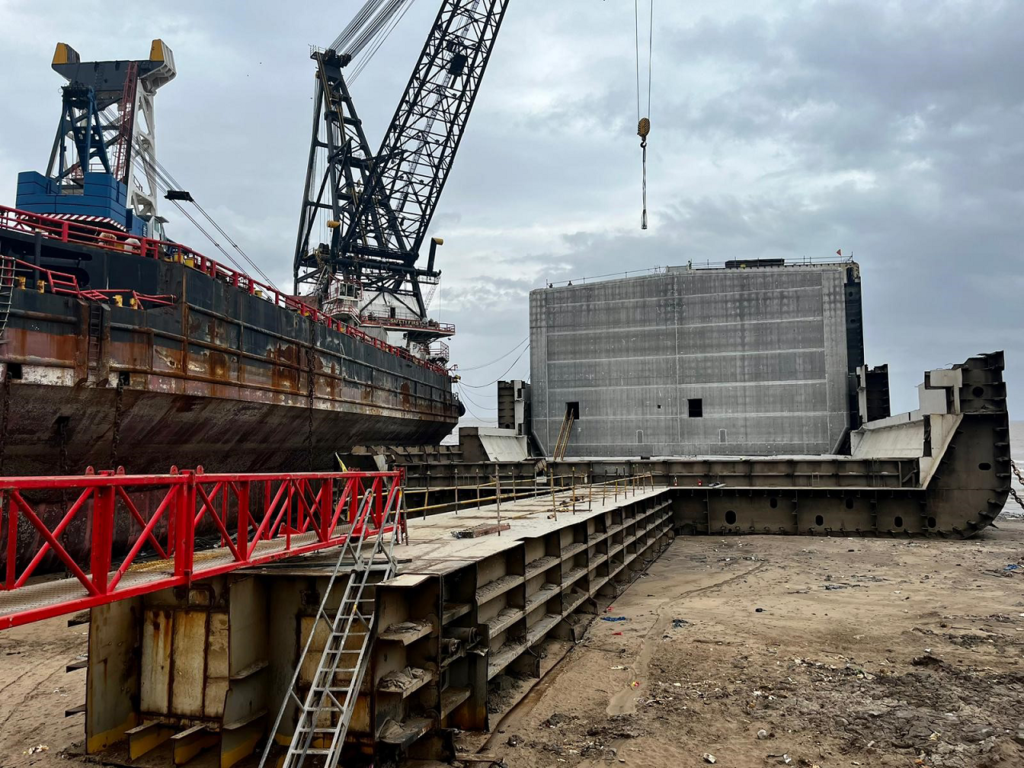
A beached ship in an Indian recycling yard.