Underwater ship repairs
A grounding in Suez, propeller repairs in the Mediterranean and semi-submersible offshore rig repairs in Australia.
When a fully laden, 300 x 50m, 207,000dwt bulk carrier suffered heavy damage from a grounding in Suez, the owners and managers’ first thought was to call Hydrex. Over the years, Hydrex has earned a reputation for being able to tackle the most challenging underwater and afloat rescue and repair operations. In this case, the ship was carrying a valuable cargo and every day it was out of action represented a huge loss to the owners.
Hydrex was contacted by the vessel’s managers requesting urgent assistance with repairing the damage so that the ship could sail again. The ship had suffered a breach of the hull, and the port side water ballast tanks (WBT) 1, 2 and 3 were letting in water. The ship was moved under state and class supervision and with a tug escort to Great Bitter Lake for an underwater survey. When the call for help arrived at Hydrex headquarters in Antwerp, the team responded immediately. Calls of this nature are answered 24/7. There is always someone on duty to take the call and start the necessary actions to begin the job.
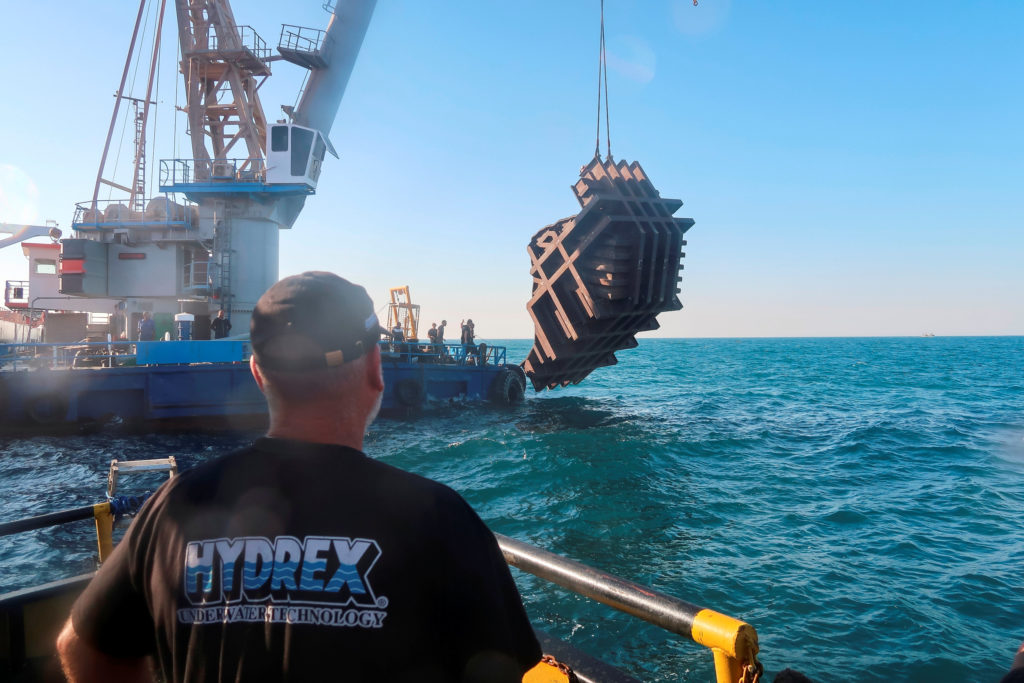
A crane barge moving the cofferdam into position
Inspection and planning
Hydrex proposed sending a team of divers to the ship in Suez to assess the damage and gather the information needed to come up with a detailed plan for repairs to enable the ship to sail to drydock. This proposal was accepted and the team rapidly mobilised.
The underwater inspection revealed and the full extent of the damage, which was quite severe. It included one hull penetration at the turn of bilge seven metres long with a maximum width of five metres and another smaller penetration of 10x5cm.
Based on the initial inspection and rough measurements, a plan was proposed to carry out precise measurements of the hull where the large damage occurred so that a cofferdam could be designed. This would then be installed to make the hull watertight so that the water ballast tanks could be pumped out.
The proposal for handling the additional damage was to arrest the crack by drilling holes and then welding a doubler plate over the large crack in the hull. The plan was approved by class (LR), and ship management gave the go-ahead to implement it. The Hydrex team took full measurements of the hull in the damaged area using a fabricated frame. The measurements were relayed to the engineers in Antwerp, who produced drawings for the yard in Egypt, where the cofferdam was fabricated. The final cofferdam consisted of a frame or shell with a flange built to the shape of the hull and insulation material to make it watertight.
45-ton cofferdam
As soon as the fabrication was completed, a Hydrex team of eight diver/welder/technicians flew back to Suez to install the cofferdam. After some modification, the massive 45-ton cofferdam was lowered into position by crane and secured against the hull with welded screw dogs, stoppers and thick seals.
With the cofferdam secured in place, an attempt was made to empty out WBT 2, but the pressure of the water was too much for the structurally weak hull, which started to cave in under the force. Evacuation of the ballast tank was halted. It became clear that the ship had suffered too much internal damage to permit the water ballast tanks to be fully pumped out. This was not something that could have been predicted or remedied with the ship afloat.
Cement boxes
To reinforce the bulkhead between the water ballast tanks, a new plan was proposed to build cement boxes and to pour in enough concrete to provide strength for the bulkheads in between the ballast tanks. But WBT 2 port could not be emptied. Part of the plan, therefore, was to lighten the ship as necessary until the class-required draft could be achieved.
Seaworthy
With the cement boxes in place, the cofferdam was fully secured and sea trials were conducted. The officers and crew of the ship were very happy with the results. A final inspection of the cofferdam was conducted and showed that all was secure and ready for sailing. The Hydrex team’s job was done and they headed home to Antwerp. Many of them had spent their Christmas working on the distressed vessel. It was a long haul with many ups and downs and unexpected twists and turns, but in the end, persistence won the day.
As WBT 2 could not be pumped out, the ship had to be partially lightered so that the class-required draft could be achieved and she could sail onto drydock. Once the ship was dry, it was possible to see the sheer magnitude of the repair job. It was the largest cofferdam ever installed in a hull repair by Hydrex. It remained firmly in place until it could be removed when the ship was in drydock and permanent hull repair could be carried out.
Conclusion
When carrying out underwater repairs, especially on an emergency basis, unexpected situations inevitably arise. The test of the divers and technicians carrying out the repairs is whether they have the knowledge and experience to think on their feet and solve the problems that come up. Teamwork and support from the technical services group at headquarters play a vital part in the successful outcome.
Hydrex is known for persistence and for getting the job carried through to a successful outcome no matter what the situation and circumstances. This was another example of these qualities and characteristics in action.
Containership repair in the Med
During a recent drydocking of a container vessel in the Mediterranean, the yard and owner noted damage to the propeller as the dock was being emptied.
There was significant damage to the trailing edge tip, which was bent aft. This damage explained some recent performance issues (overloading) the vessel had been experiencing but the crew had not been able to identify why.
Naturally, the yard was asked to repair the blade during the docking period. However, since this repair in the dry would require hot straightening, and taking off the propeller was not in the original docking scope, it quickly became quite clear this was not something they could easily address.
Wärtsilä Underwater Services (WUS) was contacted by the yard and owner as they have extensive knowledge and expertise in in-situ propulsion repairs.
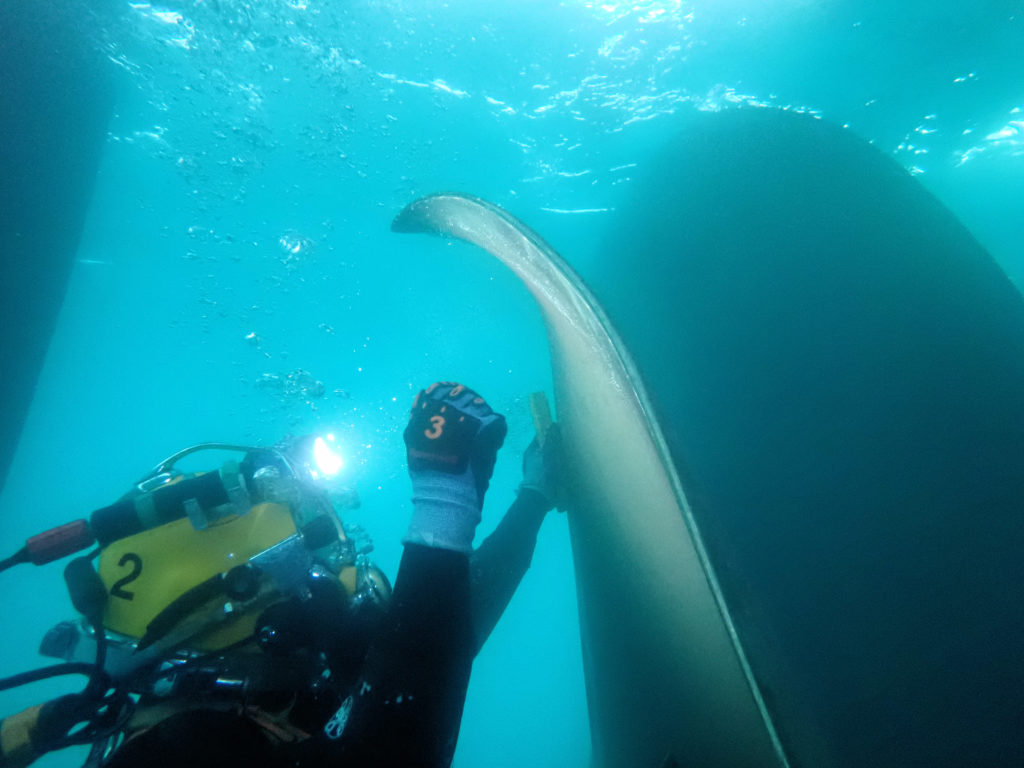
The initial damaged condition of the propeller
The solution
WUS has a range of high-capacity cold straightening presses in its arsenal that are known to resolve this type of damage swiftly and effectively.
However, they cannot be deployed in a drydock environment. The equipment is specifically adapted and designed to operate underwater. Its use on land was banned several decades ago as it imposes a health and safety risk. Carrying out the repair underwater eliminates this risk, making it an ideal solution for this type of damage.
After some discussion, it was decided to repair the propeller as soon as the vessel was re-floated.
The team mobilised to the yard a day before the undocking and all equipment was prepared on the quayside to minimise any delays.
As soon as the dock was flooded and the vessel signed off for safe operation, the team performed the repair. Inspection was not required as it had been done with the propeller still dry.
The straightening took three hours to complete, letting the vessel return to operation shortly after release from drydock.
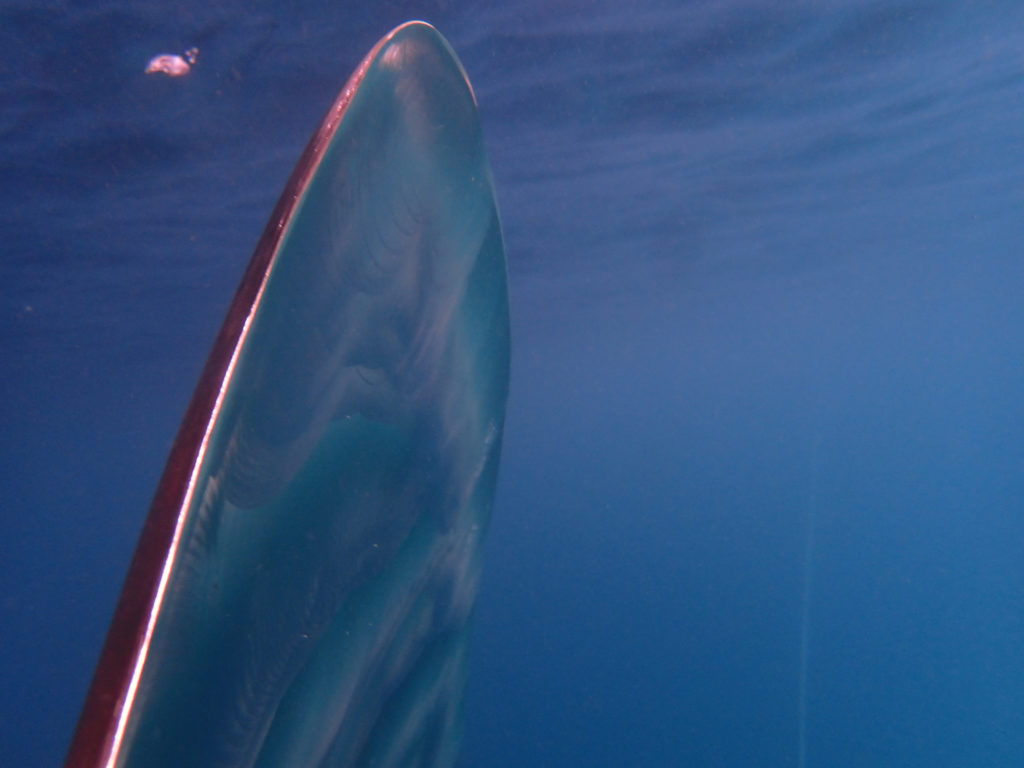
The completed propeller repair
Semi-submersible offshore rig repair
Subsea Global Solutions underwater and in-water technical repair work increased throughout the latter half of 2022. Offices in Asia-Pacific, namely South Korea, Singapore and Australia, have been busy supporting a range of offshore, cruise and commercial shipping clients, as well as local marine construction infrastructure projects.
Notable projects undertaken have included assisting a semi-submersible offshore rig with underwater damage that required ABS class-approved repairs. Subsea Global Solutions’ experienced underwater specialists apply ‘think in the water logic’ – the best and safest solution.
Prompt underwater inspection defined the extent of shell plate damage (approximately 6.5m x 3m). A skilled internal project team assembled to define the procedures for the client and approval and supporting local-content partners and plan the actual technical delivery phase. Normally, this type of situation would require repositioning the rig to an available drydock of suitable capacity and removal of the substantial DP3 thruster systems to access the dock itself – all requiring extra time and of course money for the owner-operators.
The solution
Subsea Global Solutions’ diver-technicians installed the substantial cofferdam and undertook all the relevant underwater work in conformance with the Class A requirements of AWS D3.6. Coded welders were then able to replace the damaged frames, stringers, and ultimately complete shell plate inserts, suitably keyed into the surrounding plating, safe in the knowledge that the dive team was also monitoring the cofferdam installations. All quality control checks, including vacuum and ultrasonic testing, were completed to approval of the attending class surveyor. In addition to the repair work, the unit’s future deployment required a full and thorough hull cleaning, including all niche areas, and biofouling inspection to meet rigorous Australian regulations, which was completed simultaneously.
Investment
Technical in-water repair job enquiries continue to increase, and SGS has been investing in upskilling additional in-house diver-technicians through strategic partnerships to deliver underwater wet welding and OEM shaft seal service training, both in South Korea and Singapore.
One of the benefits of scheduled biofouling inspections within a Fleet Agreement is the regular ‘eyes on’ condition of a vessel’s underwater surfaces and equipment. Shaft seals are a small but critical component in a healthy propulsion system. In Busan, South Korea, amongst the dozens of seal jobs undertaken, SGS recently completed a 1,200mm shaft seal replacement on a 400m, 20,000+ TEU containership – another record of sorts.
Providing repair and replacement of scrubber overboard (O/B) pipes is another regular job handled dozens of times a year, in both in Busan and Singapore. Scrubbers perform an essential role protecting the environment by reducing global emissions from shipping. However the immediate environment of a scrubber overboard discharge is very hard on the materials, literally eating steel, so regular inspections are advised. Solutions vary, from class-approved permanent replacement afloat to temporary solutions that keep ships sailing until scheduled drydock. These use build-up welding procedures to repair wasted spool pipes, in-place grit blasting to SA2.5, and application of a specialised coating system that can be built up to original pipe thickness.
The key to Subsea Global Solutions’ success in replacing and repairing scrubber overboard pipes is its procedures and coating system. Each pipe is measured electronically for coating thickness 1,200μm to 1,500μm, then high-voltage testing is done to confirm there are no pinholes in the coating that could allow the low PH wash discharge to make contact with the steel.
SGS provides turnkey solutions for scrubber overboard replacement incorporating class-approved wet welding procedures (AWS D3.6 Class A) for the external covers passes, coating system and verification procedures. Through its partnership with the coating manufacturer, SGS claims it is the first to offer up to a five-year warranty on scrubber overboard pipes installed afloat.
In you enjoyed this article why not read more in the latest issue of DryDock magazine