Reducing risk in maintenance management
An integrated approach to maintenance scheduling and safety management can cut onboard risk and administrative inefficiency, explains ABS Wavesight Director of Product John Hathaway.

ABS Wavesight Director of Product John Hathaway
Coordinating the scheduled maintenance that keeps ships running well is a complicated task, with multiple potential pitfalls that threaten to derail the process. It’s not just human error that can throw a spanner in the works. Sometimes the systems that ship operators use to plan maintenance fail to keep up with the inevitable stops, starts and changes as crew workload fluctuates and operational priorities shift.
With systems working in alignment however, allowing the right people to see the right data at the right time, the never-ending task list of onboard engineers can be tackled with peace of mind – saving resources wasted on re-planning and duplicated efforts while minimising the risk of safety incidents. It’s an approach that is integral to maintaining the high standards of operational efficiency and safety that the world’s biggest oil majors demand. Some of those companies spend millions on bespoke systems to meet their needs, but after a recent project with one such company, ABS Wavesight can offer similar benefits through a simple integration as part of its Nautical Systems platform.
A key challenge for conventional maintenance planning is the safety management that accompanies it. For every task there is a string of safety requirements, from the initial job safety assessment (JSA) – identifying the necessary precautions for the job type – through to the final pre-work inspection that will define extra safety measures based on conditions on the day. These various levels of assessment and approval are naturally time-limited; a JSA will not possibly take into account the true facts of a prospective work environment a month after it has been conducted.
But changes to the schedule are inevitable. It’s not simply a question of having the right parts and the right skills at your disposal, although these too need careful and adaptive planning. There’s the workload of the crew, the sailing status and location of the vessel and even weather conditions to take account of. Those delays are where a traditional approach to maintenance planning falls down. Unpicking then rethreading the string of assessments and authorisations means not only conducting inspections all over again and re-permitting work – it also dramatically increases the risk of crucial safety steps being missed.
Keeping track
With maintenance planning and safety management unconnected, it can become difficult to track safety elements when schedules change. In some cases the two systems may come from totally different suppliers, managed by different parts of the ship operating company and with no way of exchanging data. In some cases, at least one of these processes is managed manually, with written schedules or printed-out permits.
For customers of ABS Wavesight, those two elements are now connected through the Nautical Systems vessel management. The maintenance schedule can be defined from the outset and updated depending on when the work is finally ready to be carried out. It also contains pre-defined, adaptable templates for each step in the safety management process. With each update, the associated safety ‘paper trail’ moves with the schedule, and key documents remains visible and updatable from the same screen. The manual cross-checking of systems that can cause double effort is eliminated, as is the risk of crucial safety steps being missed.
For crew onboard, that integration offers new levels of flexibility in planning their workload. Through one screen the chief engineer or other project manager can view maintenance tasks, decide which ones can be done on that day, ensuring that JSAs and permits are up to date – or amending them if not – and approving the task. The clarity that this systematic approach brings can be a significant factor in preventing crew from becoming overloaded or fatigued.
There are other benefits too. Safety incidents or near misses that occur during scheduled maintenance can be thoroughly investigated thanks to a new integration with Nautical Systems’ HSQE module, meaning that essential lessons are learned, not lost in a digital archive or a pile of paper. Crew and contractors can be given full visibility of a ship’s actual, up-to-date maintenance schedule and the related safety documentation, allowing to plan their involvement – or if not involved, to see where work will be taking place.
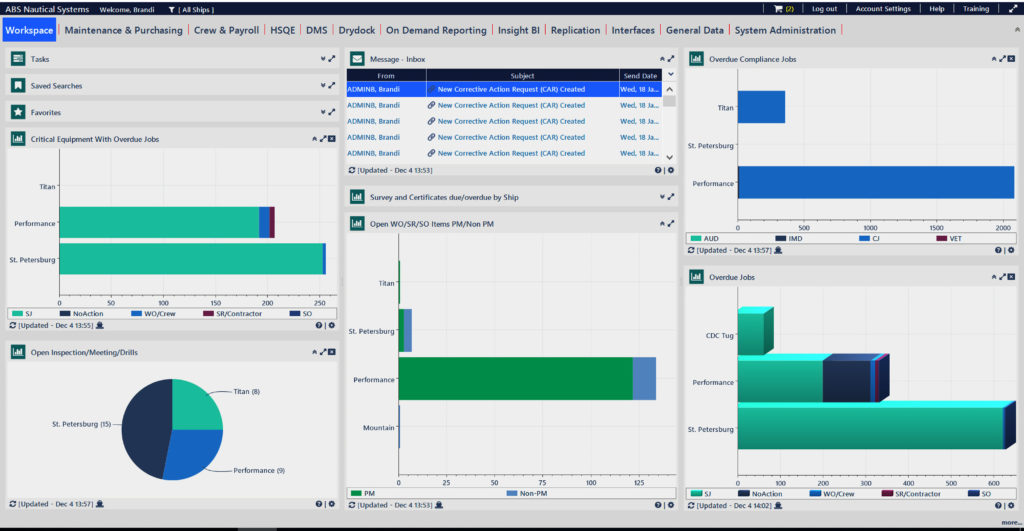
The Nautical Systems mobile app allows engineers to input outcomes or issues as they happen
Instant updates
The advantages of integrated scheduling and safety management are also evident when the work is actually being carried out. The Nautical Systems mobile app allows engineers to input outcomes or issues as they happen, rather than taking notes to be transferred into a logbook once the job is finished. As the system updates instantly, the risk of human error in logging issues during maintenance is minimised.
This kind of integrated approach can reduce bureaucracy and risk for all ship operators, but tanker operators have been among the earliest adopters. The environmental and safety risks associated with their cargoes mean that safety management is critical, and systems that improve this will offer added reassurance to charterers. The Nautical Systems integration is the result of extensive co-development with an oil major, allowing ABS Wavesight insight into the real-life planning challenges on a significant fleet. The resulting solution has now been deployed across that tanker fleet.
The combination of scheduling and safety management enabled by the new maintenance management integration also has the potential to benefit other areas. One consideration is a further integration with Nautical Systems’ drydocking management module. Drydocking is the single most expensive and extensive maintenance event in a vessel’s life, and a monumental scheduling task for both ship operators and yards. Integrating a ship operator’s digital safety management process with yard systems is bound to unlock efficiencies, safety improvements and greater transparency and visibility.
Well maintained ships are more efficient and safer, but too often maintenance can be the cause of excessive administration, delay and risk. With seamlessly integrated digital solutions, ship operators can finally give themselves the whole picture through a single window, enabling complex scheduling without compromising safety. More articles like this can be found in the latest issue of DryDock magazine