Rio Tinto selects Alfa Laval OceanGlide fluidic air lubrication
Alfa Laval will provide Rio Tinto, the world’s largest dry bulk shipper, with the OceanGlide fluidic air lubrication system. This innovative system enhances a ship’s propulsion efficiency and energy savings while sailing.
Rio Tinto has selected the Alfa Laval OceanGlide fluidic air lubrication system for one of its bulk carriers, as part of its focus to boost vessel energy efficiency and decarbonise shipping. Recognising the merits of OceanGlide in the market, the company has chosen to retrofit a Rio Tinto-owned vessel with the system to assess this energy-efficient technology for its fleet.
A smooth path to real energy savings
Introduced in 2023, Alfa Laval OceanGlide’s energy-saving capabilities have generated considerable interest from shipowners seeking to address energy efficiency and emission challenges.
OceanGlide is proven to reduce specific drag from 50–75%, which means significant propulsion power savings. This leads to lower fuel consumption and reduced CO2 emissions. The combination of these benefits positions it as a future-proof solution for improving vessel performance.
“We are delighted about OceanGlide being selected as one of the promising technologies that can support Rio Tinto in its decarbonisation journey,” says Rajiv Sarin, Head of Air Lubrication, Alfa Laval. “By providing innovative solutions, like OceanGlide, we empower our customers to achieve both efficiency and sustainability. We are proud to be part of the initiative that drives a more sustainable future.”
Efficiently reducing drag with optimised airflow
The solution combines air lubrication with fluidic technology to create an even air layer with high efficiency and little compressor power. Through this innovative approach, OceanGlide creates a more streamlined air layer on the vessel’s flat bottom by dividing the surface into segments, with each segment featuring its own fluidic band. The independent steering of each band allows a more controlled airflow to reduce friction between the hull and water. This distribution of bands into sections creates a more dynamic air layer, maximising coverage and eliminating passive cavities along the vessel’s underside.
The system requires no structural modifications, except for three to five hull penetrations of a maximum DN150. This ensures easy adaptation to existing classification certificates without necessitating any major changes or conversions, making it ideal for retrofitting as well as for newbuilds. The fluidic bands, designed with a low profile and no moving parts, can be configured underneath the ship at any shipyard with ease.
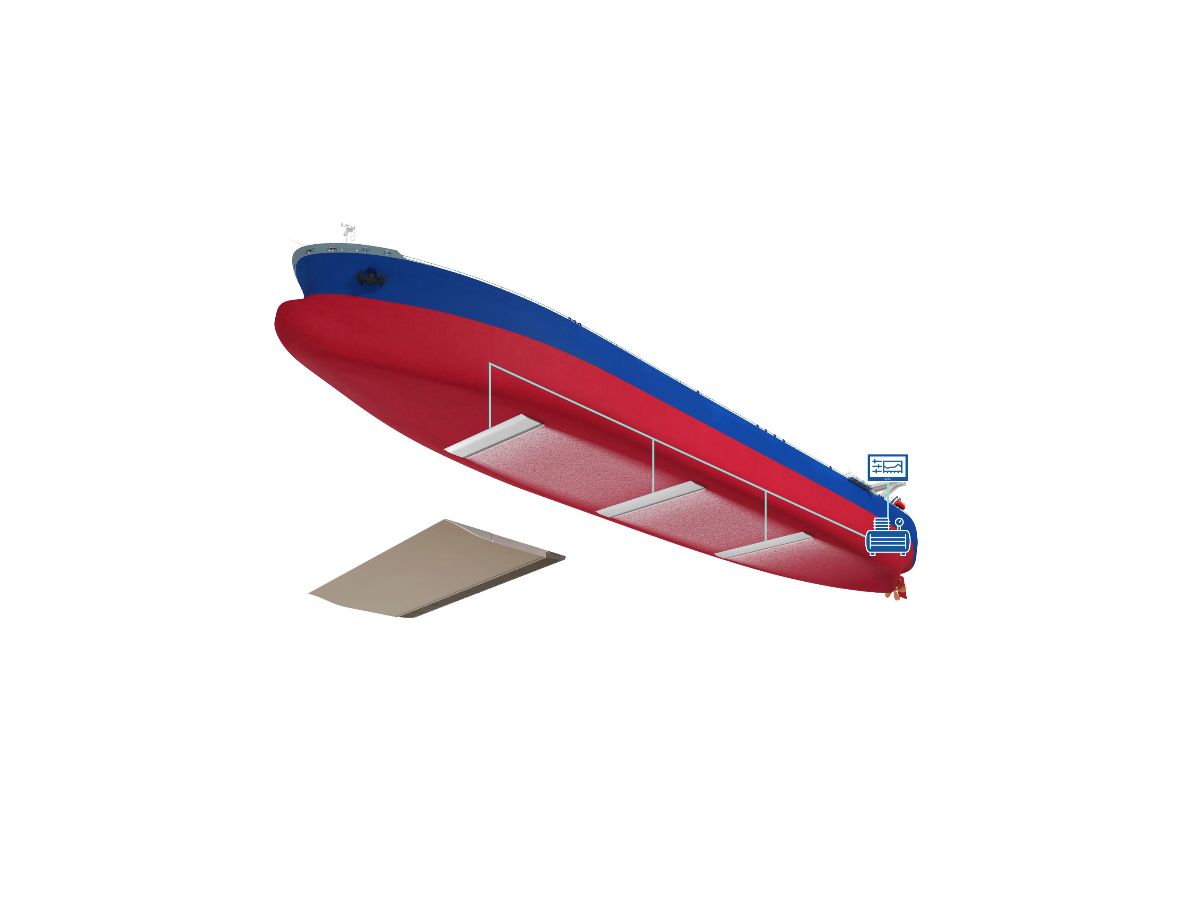
Alfa Laval OceanGlide fluidic air lubrication system